Autonomous Mobile Robots in Manufacturing
October 17, 2018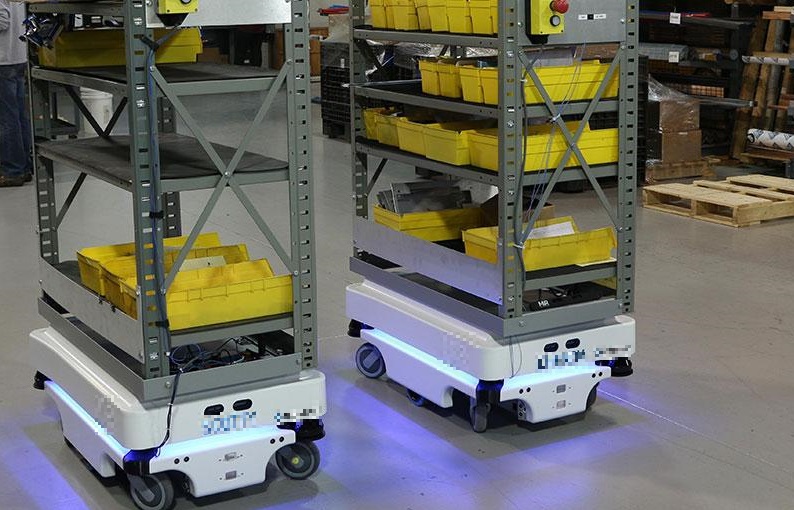
Autonomous mobile robots are becoming widely accepted in manufacturing. They are getting deployed in a broad range of environments and applications. Production processes have long been automated, but the movement of material has typically been a manual process, a gap in an otherwise automated facility. That is beginning to change with the development of autonomous mobile robots (AMRs) that move around a production facility without traditional infrastructure requirements of automated guided vehicles (AGVs).
Automated moving vehicles are having an impact on production facilities as they bring safe automation into processes that used to be done only by human workers. “We’re seeing massive shifts in automation across three trends – collaborative machines, mobile technology, and autonomous robots. Big markets are growing for these machines. A mobile robot that is safe around people without fences or boundaries sits in the center of these major trends.”Tony Melanson, VP at Aethon.
Mobile robots offer the opportunity to automate a part of the production process that is not usually done with automation. “What hasn’t been automated is the movement between cells of production. This includes raw materials, sub-assemblies, or finished goods into the warehouse,” said Melanson. “These items have traditionally been moved by people or people driving machines. For example, in electronics manufacturing, there are a lot of parts moving. People are in and among that process. Introducing a mobile machine to do this work is not trivial.”
Robots Travel Facilities Using Mapping Software
Part of the effectiveness of robots is that it can know its way around the plant, where to go when ordered to a location and it knows how to navigate around obstacles along the way. Maps are created for robots with sensors. Robots drive through facilities and measure all of the aspects – walls, doors, everything.
Part of the attraction of the automated mobile devices is the versatility and its potential coordination with other robots. One robot can perform a variety of jobs and complete tasks through the production process. Robots can be coordinated to deliver goods to different locations, right up to the person who needs the materials.
As well as closing the automation gap, robots can potentially close the workforce skills gap, since they can fill-in for hard-to-find human workers.
Humans and Robots Work Together
As with much of the advanced automation technology, robots can be integrated into the plant network. Communication coming from plant networks can determine what tasks need to be done. “In a manufacturing plant, an MES or ERP system sends a signal, and the fleet manager knows what to get and where to get it,” said Melanson. “The fleet manager figures out which is the best robot to get that material.”
For many plants, the movement of materials is the last stretch of plant processing that are still manual. Robots may be an efficient way to move material, but, are ARMs the best choice? Internal IT departments generally can not handle ARM upkeep and maintenance. Facilities need a history of various cost and analytical analysis before deciding to ditch the humans.
Spiegel, Rob. (2018). “Autonomous Mobile Robots Close the Automation Gap in Production Facilities”. Retrieved from https://www.designnews.com/automation-motion-control/autonomous-mobile-robots-close-automation-gap-production-facilities/96550703458437.