Contract/Managed Services
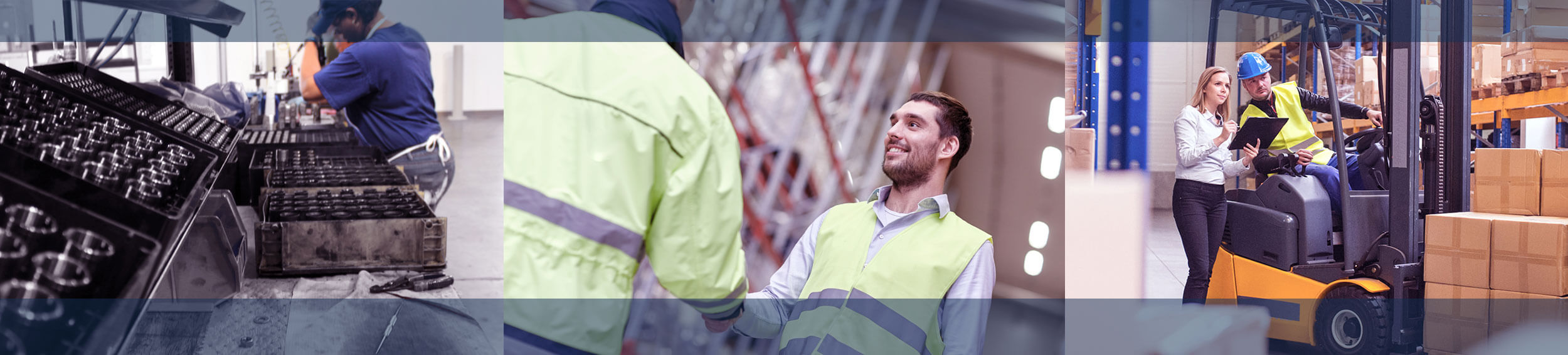
We provide simplified customer service through the management of our supplier representatives and supplier quality liaisons. The Sustained Quality model offers our customers single invoicing, timely reporting, and a single point of contact for multiple service locations.
Our goal is to help our customers resolve quality and engineering issues in the quickest, most efficient and cost effective manner possible. We provide contract engineering services and resources to support all of your operational needs. Our engineers provide the temporary support needed to close issues and drive continuous improvement before problems become major obstacles.
- Quickly establish containment to stop defective parts from reaching the customer.
- Provide detailed and actionable data to drive problem solving.
- Our engineers will focus on and conduct root cause analysis.
- We work with our customers to design and implement permanent corrective actions.
Product Launch
We provide trained, qualified and prescreened outsourced assembly support.
Contract Engineering
We provide highly qualified and prescreened outsourced engineers.
Capacity Analysis
We evaluate your production process to determine whether or not the inherent variability of its output falls within the acceptable range.
APQP/PPAP
We provide engineering staff support to complete the necessary planning and completion of the APQP/PPAP documents and processes to achieve successful program launches.
APQP Activities
Success or failure of programs often stems from the effectiveness of how well or how poorly the APQP process is executed. Utilizing the full efficiency of the APQP process provides valuable analysis of your systems strengths and weaknesses.
Our experienced engineering staff can provide timely support to complete the necessary planning and completion of the APQP documents and processes. Additionally, we can evaluate your critical suppliers’ APQP activities, ensuring due diligence has been applied and sufficient resources allocated to achieve successful program launches.
The APQP Planning Chart highlights the need to apply sufficient resources during critical peak periods of a new program. We can help with the following APQP Support Functions:
- Detailed schedule of supplier APQP actions and milestones
- Control Plan/PFMEA/Flow Chart
- Key Quality Characteristic definitions
- Gage Study and Tolerance Evaluation
- Product Validation Plan
- Supplier Inspection Standards
PPAP Approval
Our experienced quality engineers provide the necessary expertise to complete all aspects of the PPAP requirements. Our engineers have completed multiple program launches and are familiar with many customer specific PPAP submissions. Some of the documentation and sample parts that we review and prior to obtaining approval will show evidence that:
- The customer requirements have been understood
- The product supplied meets those requirements
- The process is capable of producing conforming product
- The production control plan and quality management system will prevent non-conforming product reaching the client or compromising the safety and reliability of finished parts
Customer Liaison
A consistent presence at the customer facility provides measurable benefits in customer satisfaction, issue resolution and communication. Our CSE’s work can prevent items from escalating. Fully scalable resources can be on site a few hours a week, or with a full technical team to support an escalating issue.
A Sustained Quality representative can:
- Perform quality problem analysis
- Communicate corrective action to customer
- Coordinate containment activities
- Provide on-site launch support for startup programs
Supplier Management/Audits
One point of contact. Supervisory authority and systematic review of interactions with third party organizations.
Technical/Rep/Liaison
Specialized on-site customer support providing quality analysis, corrective action, launch support and containment activities.
Ask Representative for additional servicing locations not listed.
Adrian, MI
Arlington, TX
Belvidere, IL
Canton, MS
Chattanooga, TN
Cleveland, NC
Clyde, OH
Denton, TX
Detroit, MI
Elizabethtown, KY
Fletcher, NC
Flint, MI
Fort Wayne, IN
Fremont, CA
Garland, TX
Glasgow, KY
Howell, MI
Lansing, MI
Marion, OH
Mishawaka, IN
Orion, MI
Shelbyville, TN
Spartanburg, SC
Tuscaloosa, AL
Wentzville, MO
Various Locations:
Throughout USA, Canada and Mexico