OEM Services
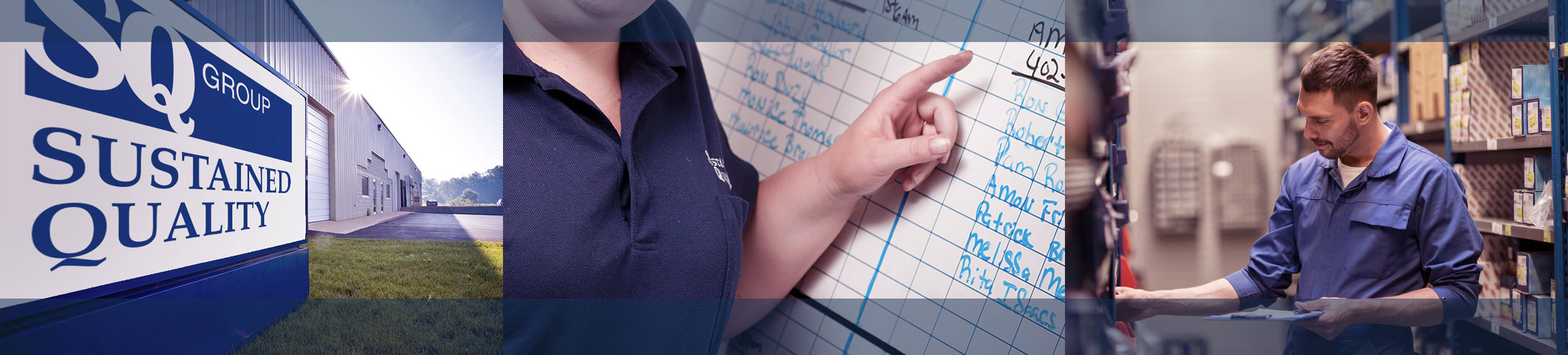
SQ manages regional distribution centers for an OEM’s service parts supply chain, annually ranking in the top two spots for customer service and performance.
GM QSB Plus Training GM
Cs2-Approved Vendor
Montgomery, AL
West Point, GA
Tuscaloosa, AL
Huntsville, Al
Princeton, In
Georgetown, KY
Newnan, GA
Decherd, TN
Oxnard, CA
Buffalo, WV
Charleston, SC
Sustained Quality assists companies that manufacture vehicles using the components and subassemblies that Tier 1 suppliers provide to them.
Full-Service Quality Management
Sustained Quality oversees all Original Equipment Manufacturing activities and tasks needed to maintain a desired level of excellence.
- Receiving Inspection/Line Call Support
Analyzing pre-production process or parts for OEM. - Sole Source Quality Inspection
Analyzing OEM unique parts having singular characteristics or performance capabilities. Selected OEM has 100% of the business for part(s) although alternative suppliers are available. - Engineering Change Rework
Implementation of OEM change(s) to specific design(s). - Yard Campaign Management and Reporting
OEM production time organization and analysis. - JD Power Double Check Programs
One of the only sources of consumer ratings based on independent and unbiased feedback from a representative sample of verified product and service owners. - Supplier Quality Engineering Services
OEM part developing or solving issues.- Launch Readiness Support
OEM project management improving readiness and process to prevent post-production issues. - Model Year Build-Out Management
Tracking and reporting of product number/code.
- Launch Readiness Support
- Port Quality Inspection
Analyzing OEM parts at harbor.
Quality/Quantity Monitoring (SSC, Q; Help, CSI/CS2, Etc.)
Monitoring and reporting of OEM data quality standards across the data management.
- Current Provider for “6” OEM Customers 10% of market place.
- Real Time Data Monitoring No delay of OEM data analysis.
- Hourly Production/Delivery Reporting Hourly OEM data updates.
- Corrective Action Implementation and Validation Improvements to OEM’s process taken to eliminate cause of non-conformities or undesirables.
Service Parts Management
OEM spare part support.
- Gold Standard Performance
The level of measuring sustainable certified standards.- KPI Metrics
Analyzing and reporting Key Point Indicators for the success of OEM projects, programs, products and other initiatives.- Quality
Analyzing and reporting OEM defined KPI for quality standards. - Accuracy
Analyzing and reporting OEM accuracy KPI. - Productivity
Analyzing and reporting OEM productivity KPI.
- Quality
- KPI Metrics
- Quality Inspection Support
Visual analysis and reporting of OEM parts for defects during production or in warehouse. - Warehouse Management
Inventorying and storying parts and components in fully functional Sustained Quality warehouses and delivering to meet production schedules. - Material/Inventory Management
Part and component management at OEM facility or Sustained Quality warehouse to find innovative solutions to fit logistic needs. - Distribution
On time delivery of warehoused parts and components to fill production needs.