Laser Welding Technique Addresses Process Issues
May 28, 2019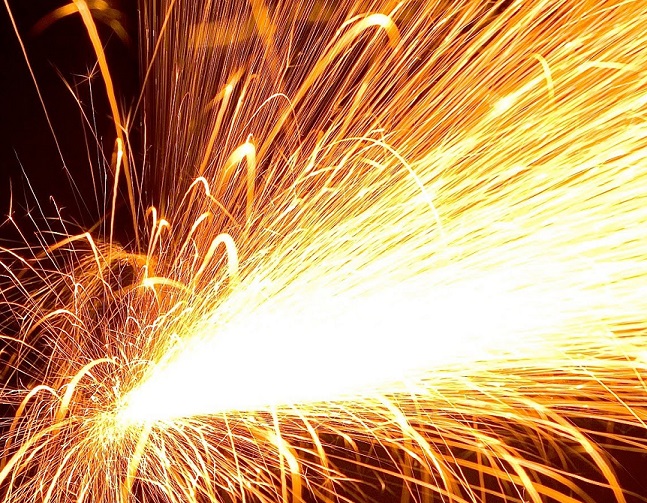
The automotive industry is witnessing a demand in higher standards for passenger safety, vehicle performance and fuel economy. The problem: Advanced high-strength (AHS) steels, commonly used in car body structures to absorb impacts, become brittle and sometimes break due to welding and hot stamping processes. A solution is in sight.
European scientists are developing a new ‘pulsed’ laser system, similar to the 2018 Nobel Prize in Physics winner, to cut and shape ultra-high-strength industrial materials that are notoriously difficult to process at unimaginable speeds, while producing considerably less waste.
The new laser will be powerful enough to cut the hardest boron steel used in car construction at one cubic centimeter per minute – over a thousand times faster than existing technology that currently ablates steel at one cubic millimeter per minute.
Exerting an average power of 2.5kW, or 100kW in a single pulse, and with repetition rates up to 1GHz (or 1 billion cycles per second – a thousand times more than the current 1MHz upper limit), the laser will have the control and refinement to etch molds for vehicle parts at micron-scale accuracy as well as micro-weld dissimilar metals for solar thermal absorbers.
Commonly used in laser eye surgery, pulsed lasers send out short blasts of energy, or ‘pulses’, in tiny fractions of a second. The pulses in this new laser are so fast that their duration is measured in femtoseconds – a femtosecond compared to a second is in the same ratio as one second to 32 million years.
Aiming to improve car manufacturing speed and efficiency, while reducing the potential production costs and environmental impact, the new pulse laser system has received a 5 million development grant from the European Commission.
Commonly used boron steel is used in car bodies because of its super strength. It is so durable that it is often difficult to cut or shape. The processes used to ensure its durability usually remove many of the steel’s fundamental properties, such as the workability.
Although boron steel can be cut with a plasma arc torch, (a tool that cuts using high pressure, accelerated jet of hot plasma), this can instantly heat the metal to over 1,200º Fahrenheit and is not as precise or as quick as a pulse laser.
Going by the acronym ‘PULSE’, the consortium behind the powerful new laser draws on expertise from eleven research institutions and industry partners from six different European countries and is coordinated by Tampere University in Finland.
Project coordinator, Dr Regina Gumenyuk said:
“While ultrashort-pulse laser (USPL) technology has been around for decades, breakthroughs have meant it has become something of a buzzword, being awarded the latest Nobel Prize for physics, and increasingly being deployed in industrial production.”
“Laser technology exists today that can cut boron steel, but it is far too slow for any large scale production”.
“By harnessing the unique characteristics of patent protected tapered double-clad fiber amplifiers power-scaled multi-channel laser, the PULSE project will create unparalleled high-power beam qualities.
“PULSE is committed to improving manufacturing, but also reducing the impact on the environment, therefore we can confirm that a 10% reduction in waste products is certainly achievable”, Dr Gumenyuk said.
The laser system will enable an improved digital design to lighten vehicle chassis weight with benefits to fuel economy and increase the range of electric vehicles.
The consortium expects a prototype to be ready by 2021.
The PULSE consortium is made up of partners from six countries:
- United Kingdom (Aston University and Modus Research and Innovation Limited);
- Finland (AMPLICONYX OY);
- Germany (LUNOVU Gmbh and Hochschule Mittweida);
- Greece (Nanotypos OE, Foundation for Research and Technology HELLAS, and Prime Laser Technology Iliaka Systimata Thermansi Anonimi Viomichaniki Emporiki Etaireia);
- Italy (Centro Richerche Fiat SCPA and Onostampi SRL);
- Latvia (Ceram Optec Sia)
(2019). Retrieved from https://www.novuslight.com/powerful-new-laser-to-boost-automotive-manufacturing_N9335.html.