Explaining FMEA & How to Perform It
January 15, 2023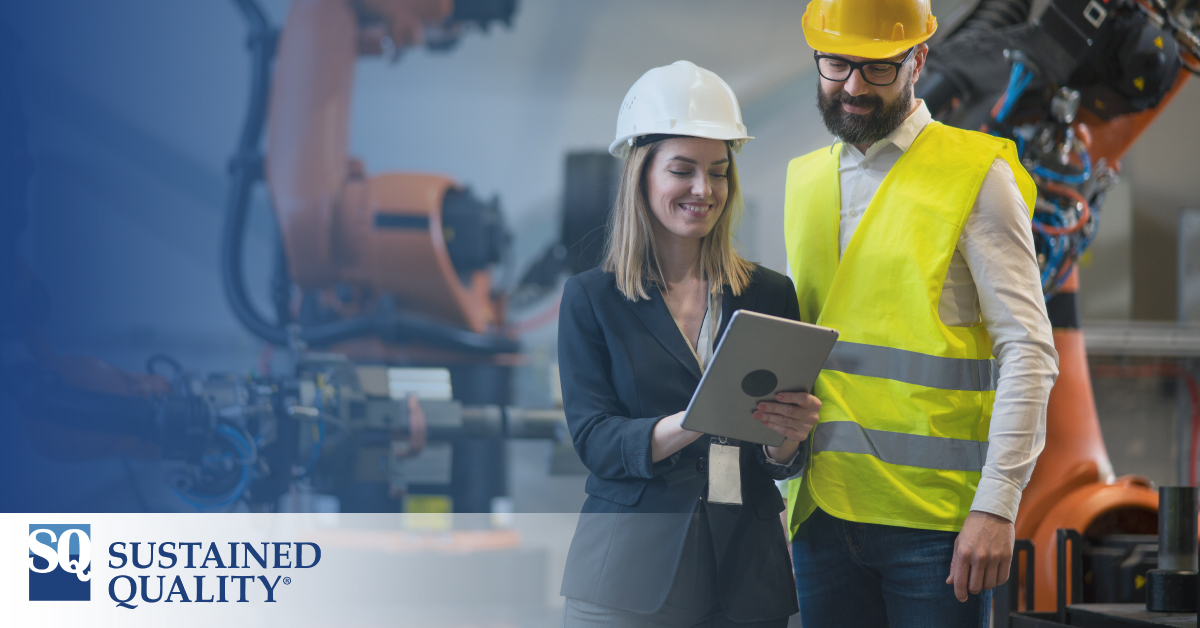
Failure mode and effects analysis (FMEA) optimizes the engineering of a process or product. Through applied knowledge and experience, professionals review the design of the process or product and assess the potential for failure mode.
Businesses can resolve potential issues uncovered. This elevates the quality and safety of the finished product for the consumer.
Learn about FMEA and how to perform it to elevate your customer experience.
Explanation of Failure Mode and Effects Analysis
FMEA is a structured approach to finding potential failure modes in the design of a process, product, or service.
- Qualitative and systematic methods are used to identify potential failure modes and potential causes.
- Data tracked on a spreadsheet is used to make decisions to mitigate potential failure modes.
- Effects are failure modes that can result in defects, waste, or unsafe outcomes for the consumer.
When to Perform Failure Mode and Effects Analysis
- Designing or improving a process, product, or service
- Making a process, product, or service perform differently
- Aiming to understand the underlying failure of a process
- Working toward quality improvement for a process or product
- During the lifetime of a process or product to optimize results
How to Perform Failure Mode and Effects Analysis
Select the relevant participants to determine the potential failure modes.
- FMEA designers, process owners, suppliers, practitioners, and end customers may be involved.
- Brainstorm to identify the systems, processes, components, and functions that could go into failure mode.
- Uncover the potential causes of potential failure modes.
- Aim to elevate the quality and reliability of the finished product.
Use three criteria to assess each potential failure mode and effect:
- The severity of the effect on the consumer includes all standards relevant to the industry. Examples include safety standards, production continuity, loss of business, damage to the company’s reputation, and impact on the environment.
- The frequency of the problem ranks the probability of each failure mode during the estimated lifetime of the process or product.
- The detection level of the problem ranks how easy it is to find and take action to prevent failure mode.
Determine a ranking scale from 1 (very low) to 10 (very high).
- Rank the severity, frequency, and detection of each potential failure mode.
- Use the data to qualify the decisions about the ratings.
- Multiply the severity, frequency, and detection rates for each potential failure mode.
- The answer determines the risk priority number (RPN) for the potential failure mode.
Set the FMEA priorities.
- Create the list in descending RPN order.
- This setup shows what the participants should focus on first.
- The lower-priority issues can be resolved later.
Agree on what the priorities are.
- Take corrective action to reduce or eliminate each potential failure mode.
- Assign each action and targeted completion date.
- Meet again to determine and reassess each potential failure mode.
- Rescore each potential failure mode according to the criteria.
- Improve the effectiveness of the corrective actions.
Do you need support resources?
Sustained Quality provides support resources focusing on quality containment and customized solutions for quality control challenges. Reach out to us today.