Advanced Electronics Need Quality Standards All Their Own
February 13, 2019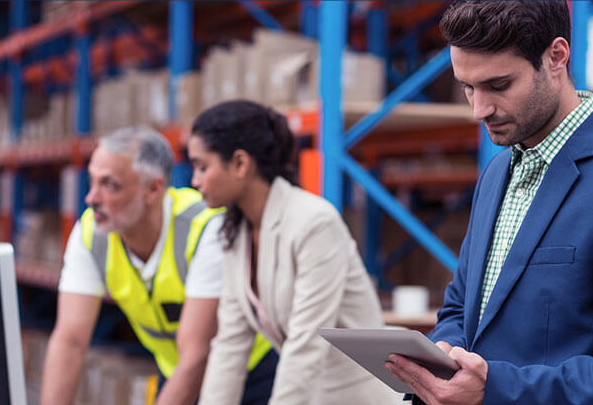
Automakers are right in demanding quality, but the same quality methods and strategies can not be used in automotive advanced electronics as other categories.
A 2018 report by J.D. Power showed that overall car reliability is improving year over year. But it also showed that audio/communication/entertainment/navigation (AECN) remains the biggest source of complaints for the third year in a row. Meanwhile driver-assistance issues are increasing 20% per year. That number is still low, because there are not too many of these systems on the road compared to the total number of cars, but those numbers likely will rise significantly as these technologies show up in more vehicles.
Automakers have responded to these complaints by strengthening their failure in time (FIT) requirements for suppliers. Rather than parts lasting 7 to 10 years, they now demand zero defects for 18 years. Alternatively, they are demanding zero incidents per a part, which allows suppliers some wiggle room because it means that redundancy or possibly a fail-over could reduce those incidents to zero.
But their solution to these complaints is basically a knee-jerk reaction to one of the most fundamental shifts in the history of automobiles. Moreover, it shows a disconnect between automakers and tier 1 and tier 2 suppliers, and modern electronics. Automakers need to rethink their business model.
Prior to Tesla, all of the big improvements in automotive engineering were weighted much more heavily on the mechanical side than electrical—overhead camshafts, anti-lock brakes, fuel injection, airbags. The chips used in these systems are primitive compared to the electronics in a robotic vacuum cleaner, and they do not wear out quickly because many of them consist of basic circuitry developed at 0.25 micron processes or larger. They are heavily insulated to protect them from engine noise and vibration, and the lines/spaces are so large that heat is not a major problem.
Adding advanced electronics, including 7nm AI systems for driver assistance and autonomous driving, requires a whole different approach. For one thing, these systems are so new that no one has ever actually observed how they behave over time. And while simulation and accelerated testing are helpful, try simulating a 7nm AI chip used intermittently on a rutted dirt road in the Mojave Desert, or one used pre-monsoon season in Bangalore when humidity is at its highest.
There are solutions to these problems, but they eat into profits. Redundancy costs more than fail-over. Squeezing suppliers costs less than adding in-circuit monitoring and continual testing of more components.
Carmakers need to be thinking like high-tech companies. There are always solutions to quality problems, but they are not always simple in electronics. And demanding that advanced electronics need to have defectivity rates in the parts per trillion range indicates how much carmakers still need to understand.
If you need assistance with your quality control, call 615-953-1907, email ContactUs@Sustained-Quality.com or complete this contact form to be put in contact with a representative in your area.
Sperling, Ed. (2019). “The Paradox of Automotive Electronics”. Retrieved from https://semiengineering.com/the-paradox-of-automotive-electronics/.